Preventive Strategies: Maintenance to Avoid Issues
Table of Contents [ ]
- Maintenance to Avoid Issues
- Welcome to Plastic Card ID
- Understanding Your Card Printer's Needs
- Preventing Card Jams and Misfeeds
- Quality Assurance Through Rigorous Testing
- Spotting Signs of Wear and Tear
- Creating a Tailored Maintenance Schedule
- The Role of Professional Maintenance Services
- Join Plastic Card ID for Unmatched Support
Maintenance to Avoid Issues
Welcome to Plastic Card ID
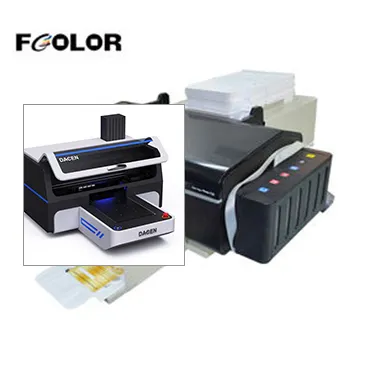
Maintaining card printers is crucial for the seamless operation of many businesses, educational institutions, and various organizational settings. Plastic Card ID , a leader in providing comprehensive printing solutions, offers a valuable guide on maintenance to avoid common issues with card printers. By following our insights, clients can ensure the longevity and reliability of their printing systems, guaranteeing their operational continuity. Remember, should you have any questions or need to place new orders, Plastic Card ID is here to serve you nationally. Just reach out to us at 800.835.7919 , and we'll provide you with all the support you need.
Understanding Your Card Printer's Needs
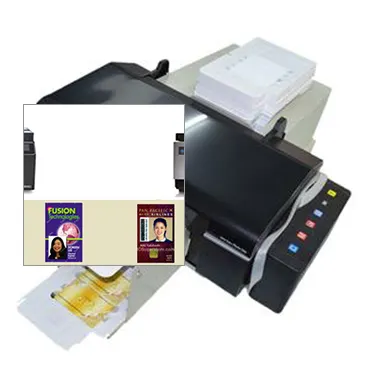
Just like any high-functioning device, card printers need attention and care to operate at their best. By staying proactive about your printer's maintenance, you can prevent the majority of issues that could lead to downtime and additional costs. The first step is understanding the different parts of your card printer and how they work together.
Regular cleaning and calibration are critical for consistent quality and performance. Overlook any of these aspects, and you may face a host of preventable issues, such as card jams and poor image quality. Let's dive into a deeper understanding of what makes your card printer tick.
Cleaning Cycles Are Key
The importance of regular cleaning cannot be overstated. Dust and debris can accumulate inside your printer, leading to various problems with card feeding and print quality. Establishing a regular cleaning schedule is a simple yet effective way to enhance printer reliability.
Your card printer typically comes with cleaning kits. These kits include everything needed to maintain the different components, from the printhead to the card feeding mechanism. Adherence to manufacturer-recommended cleaning cycles is also a testament to your commitment to upkeep.
Printhead Protection Practices
The printhead is arguably the heart of your printer. As such, it demands special care. One common issue that can occur with card printers is damage to the printhead due to mishandling or debris buildup. Handling it with caution and cleaning it as per guidelines can save significant costs in the long run.
Remember, replacing a printhead can be costly, but with proper care, you can extend its life significantly. At Plastic Card ID , we can guide you through the proper maintenance procedures and provide the necessary supplies to keep your printer's printhead in top condition.
Calibration Is Crucial
Card printers have various sensors and settings that need to be calibrated periodically to ensure optimal performance. Calibration can align the printing elements with the card's dimensions and material, ensuring that each print job is executed flawlessly.
Uncalibrated printers may produce cards with misaligned text or images. By following our comprehensive guide, you'll learn how to calibrate your printer correctly, ensuring you get the best results with every print job.
Preventing Card Jams and Misfeeds
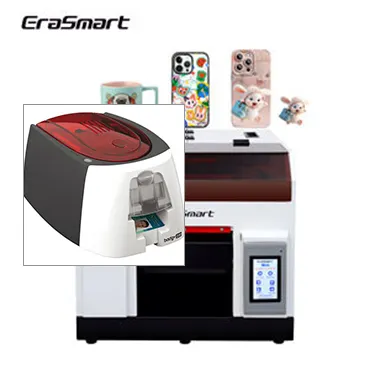
Card jams and misfeeds are two of the most common problems encountered with card printers. Not only are they frustrating, they can also interrupt your workflow. Prevention is the best approach, and it begins with understanding how these issues occur and the steps you can take to avoid them.
Most card jams are due to dirt and debris clogging the card feed path or to using incompatible card stock. Ensuring the cleanliness of your printer and only using recommended card materials are straightforward steps to mitigate these risks.
Choose the Right Cards
Using the correct card stock is crucial for preventing jams and misfeeds. Cards that are too thick, too thin, or have irregular surfaces can cause issues. It's important to refer to your printer's specifications and choose card supplies that meet these requirements.
At Plastic Card ID , we can help you select the most suitable cards for your printer, thus reducing the likelihood of problematic printing scenarios. By choosing high-quality card stock, you are also ensuring the clarity and longevity of your printed cards.
Card Path Integrity Checks
Regularly inspect the card path for any signs of wear or accumulation of debris. Any foreign material in the card path can misalign cards and cause jams. Simple visual checks and cleanings can keep the path clear and functional.
At Plastic Card ID , our maintenance guide provides detailed instructions for inspecting and cleaning your card path. Our goal is to help you maintain smooth and uninterrupted card production.
Printer Environment Considerations
The location of your printer can greatly influence its susceptibility to issues. Operating in a clean, dust-free environment will reduce the chances of dirt and debris entering the system. Understanding the importance of the printer environment, we provide suggestions on optimal setup locations.
Take care to position your printer in an environment that promotes its operational wellbeing. Plastic Card ID can offer advice on the best practices to minimize exposure to environmental factors that may cause jams or misfeeds.
Quality Assurance Through Rigorous Testing
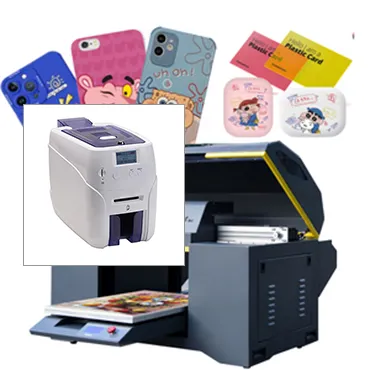
Quality assurance is vital in maintaining the performance of your card printer. No preventive maintenance guide is complete without a testing regimen. Such regimens help in catching potential issues before they impact your operations.
Regular testing of print quality, card feeding, and encoding functionality can pinpoint areas that may require attention. At Plastic Card ID , we understand that quality assurance is more than just a step it's an ongoing commitment.
Print Quality Check-ups
Scheduling frequent print tests allows you to assess the color accuracy, sharpness, and overall clarity of your printed cards. Discrepancies can often be resolved through cleaning or calibration, ensuring consistent quality in your card production.
These testing routines can be as simple as running a 'self-test' provided by the manufacturer, which prints a sample card for you to evaluate. Inspecting these test cards is part of the essential maintenance practices that Plastic Card ID champions.
Feeding Mechanism Assurance
The feeding mechanism of your printer is its lifeline for steady production. Regular testing ensures that cards are being picked and transported through the printer correctly. Any inconsistency noticed during these tests should be addressed promptly.
At Plastic Card ID , our maintenance guide outlines a systematic approach to testing the card feeding mechanism. We also provide maintenance kits and expert guidance to help you perform these checks efficiently.
Encoding System Checks
If your card printer has encoding capabilities, it's paramount to test these features routinely. Proper function of magnetic stripes, smart chips, and RFID technology ensures that your card's security features remain intact and operational.
Plastic Card ID provides detailed instructions for testing and maintaining your printer's encoding system. Following these guidelines will contribute to the integrity and functionality of your encoded cards.
Spotting Signs of Wear and Tear
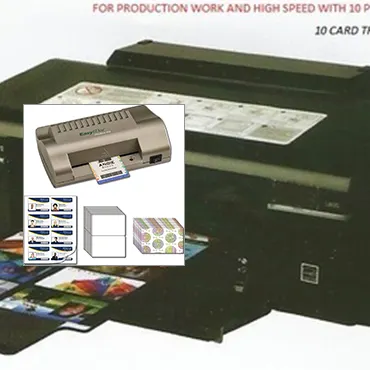
Over time, just like any other piece of equipment, card printers will show signs of wear and tear. Recognizing these signs early on can prevent small issues from becoming major problems. Visual inspections are an essential part of any maintenance schedule.
Pay close attention to parts like rollers and ribbons which can wear out over time. By replacing these components before they fail, you can ensure consistent operation without interruption. Stay one step ahead with Plastic Card ID 's detailed maintenance guides.
Ribbon and Supply Management
Printer ribbons are consumables that need regular replacement. Using high-quality ribbons and storing them properly can extend their life and improve print quality. Keep an eye on supply levels and reorder when necessary to avoid running out mid-task.
At Plastic Card ID , we offer a wide variety of supplies and can guide you in managing your inventory effectively. We're just a phone call away at 800.835.7919 for new orders and supply management assistance.
Roller Health Checks
The rollers are critical for moving cards through the printer. Over time, they can become coated with residue or start to wear down. Regular cleaning and checking for wear can help maintain their effectiveness.
We offer specialized cleaning tools and instructions on how to keep your printer's rollers in pristine condition. Following Plastic Card ID 's advice can equate to fewer card jams and superior print output.
Upgrading Firmware and Software
Like any modern technology, card printers benefit from software and firmware updates. These updates often include improvements in performance and security. Keeping your printer's software up-to-date is an important aspect of preventative maintenance.
We can assist you with the update process to ensure your printer is running the latest firmware and software versions. Plastic Card ID 's support extends beyond hardware and into the digital aspects of your printer's functionality.
Creating a Tailored Maintenance Schedule
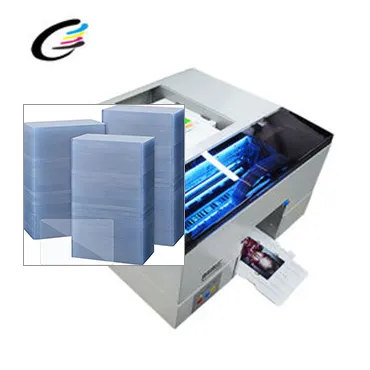
Each business has its own specific needs when it comes to card production volume and usage patterns. Creating a tailored maintenance schedule can address the unique requirements of your operations. A customized approach ensures that your printer receives the attention it needs when it needs it.
Plastic Card ID encourages clients to develop a planned maintenance routine based on our guide, which can then be adjusted according to individual demands. Let's consider how to formulate a schedule that works for you.
Assessing Print Volume and Usage
Understanding your average print volume is the first step in creating an effective maintenance schedule. Higher volumes might necessitate more frequent servicing, while lower volumes may require less frequent but more thorough sessions.
With Plastic Card ID 's help, you can translate your usage patterns into a maintenance timeline that reduces the likelihood of unexpected failures. Regular servicing aligned with your print volume can optimize printer lifespan and performance.
Considering Environmental Factors
The environment in which you operate your printer can significantly influence maintenance needs. Dusty or humid conditions may demand more rigorous cleaning routines to ensure component integrity and reliable performance.
Our expert team can help assess your work environment and suggest adjustments to your maintenance schedule. By taking environmental factors into account, you can proactively prevent many common printer issues.
Customizing for Printer Model and Age
Printer maintenance also varies by model and age. Newer models might require less frequent checks, while older, heavily-used printers might need more regular attention. Identifying and understanding these nuances is part of establishing your upkeep practice.
At Plastic Card ID , we factor in the specifics of your printer's model and age when advising on maintenance schedules, helping you achieve the best possible performance regardless of your hardware's lifecycle stage.
The Role of Professional Maintenance Services
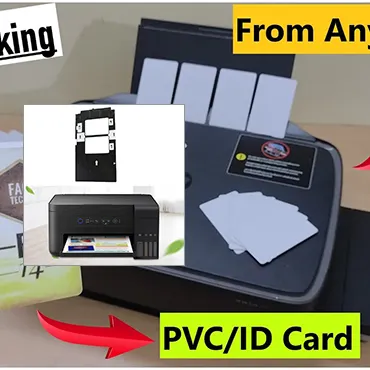
Professional maintenance services play an important role in ensuring your card printer operates at its fullest potential. At Plastic Card ID , we offer expert services to complement your in-house maintenance efforts.
Relying on professionals can provide specialized insights into the condition of your printer and help prevent complex issues. Our technicians are trained to detect subtleties that might be overlooked during routine checks.
Comprehensive Maintenance Plans
Plastic Card ID offers comprehensive maintenance plans that cover everything from routine cleaning to detailed inspections and part replacements. These plans are designed to fit seamlessly into your operational schedule without disrupting your workflow.
The advantage of a well-structured maintenance plan is peace of mind, knowing that your printer is in the hands of experts. With us, you are assured of priority service, quality parts, and consistent support.
Expert Troubleshooting
When issues arise, having a team of experts who can promptly troubleshoot and resolve printer problems is invaluable. Our technicians possess a deep understanding of card printer systems and are equipped to deal with a wide range of issues swiftly.
By choosing Plastic Card ID for your card printer maintenance needs, you benefit from our technical expertise and quick response times. Our goal is to minimize downtime so you can focus on what you do best.
In-Person and Remote Assistance
Whether you require on-site service or remote support, Plastic Card ID has various options to assist you. Our services are designed to be flexible and responsive to your needs, wherever you are located nationally.
For professional guidance or any inquiries, don't hesitate to reach out to us. Our team is easily reachable for new orders or any questions at 800.835.7919 , providing nationwide service with a personal touch.
Join Plastic Card ID for Unmatched Support
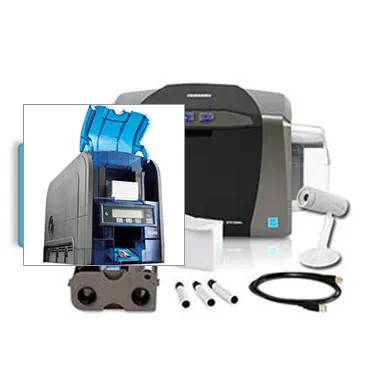
At Plastic Card ID , we dedicate ourselves to offering unmatched support for your card printer maintenance needs. Our proactive approach and comprehensive maintenance guide exemplify our commitment to supporting your operational continuity.
From creating tailored maintenance schedules to offering professional servicing, we have the knowledge and resources to help you avoid the common issues associated with card printers. By choosing Plastic Card ID , you choose reliability, efficiency, and peace of mind.
For any assistance, new orders, or questions related to your card printer maintenance needs, remember that Plastic Card ID is just a phone call away. We're proud to serve everyone nationwide and are always here to support your business. Connect with us today at 800.835.7919 , and let us ensure the longevity and dependability of your card printer.
Previous Page